
Newsletter
Special Interest Group of the American Association of Bioanalysts (AAB)
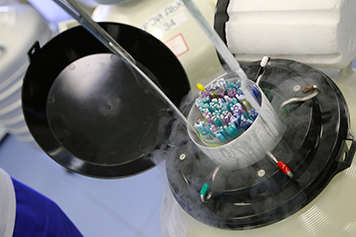
What is the Goal of Instrument Qualification?
Carli W. Chapman, ELD/TS(ABB)
Instrument qualification is “a series of processes which establishes documented evidence which provides a high degree of assurance that a specific process will consistently produce a product meeting its predetermined specification and quality attributes.”1
Wow – that sentence is a mouthful! Let’s break it down:
- Series of processes (aka installation, operational and performance qualifications)
- The processes provide a high degree of evidence (documentation)
- The equipment meets the specifications you require
- The equipment will consistently work the way you expect it to
Validation is how well a product meets your specific needs and verification is testing that product to confirm the instrument meets your specific needs. Verification and validation are independent procedures that are used together for checking that a piece of equipment meets specifications and that it fulfills its intended purpose. Verification and validation results in qualification.
Regulatory and certifying bodies have requirements for equipment qualification and it is just good laboratory practice. International Organization for Standardization (ISO), Clinical Laboratory Improvement Amendments (CLIA), Center for Medicaid Services (CMS), Food & Drug Administration (FDA), College of American Pathologists (CAP) and Departments of Health (DOH), all have equipment qualification requirements.
As an example, we are going to use an incubator purchase to detail equipment qualification.
If you were to purchase a new Sanyo MCO-5M incubator you would need to specify what configuration you want. The gas sensor may be thermo-couple or infrared technology, you may opt for UV sterilization capabilities or right- or left-handed doors. This is known as the “user requirement specification (URS).”2
You want to confirm that the equipment you received meets the specifications you ordered and functions the way you expect it to.
What does the series of processes look like? Post-purchase qualifications can be divided into three major categories:
- Installation qualification – documents installation according to both URS and Design Qualification (DQ)
- Operational qualification – documents the functionality of the equipment
- Performance qualifications – documents the equipment performance
Installation qualifications (IQ)
Any operating manual for any piece of your equipment in the laboratory will have installation qualifications. From our MCO-5M incubator example, the installation instructions include the environmental conditions the equipment has been determined to function under (Indoor use, voltage, voltage fluctuations, humidity, etc.). These working and installation conditions are determined by the manufacturer and they are listed in the operating instructions. You would not be expected to determine these types of installation qualifications. This would be supplied to you by the manufacturer of your equipment.
The next section of the installation will have things about the site installation. For example: do not expose to direct sunlight or separate from heat sources. Use only in a well-ventilated area. Place only on a strong level floor. Again, these instructions will be in the operating manual and determined by the manufacturer of the equipment.
Installation instructions will detail how to install your new incubator. It is optimal to have the vendor or manufacturer install purchased equipment but if this is not possible, there are specific instructions for installation. The result of installation qualification is:
- Proper configuration and installation – you have received the equipment you specified, and it is installed in your laboratory. In our incubator example, you have received the incubator and installed it on a level floor in an area with good ventilation and proper power supply.
- Verification that along with the equipment any sub- or ancillary systems have been delivered, installed and configured. The equipment has been configured for your use. In our incubator system, this would be setting the desired CO2/O2 concentrations and temperature, as well as Installation of the ancillary monitoring system.
- Documentation of calibration – Instruments should be calibrated with known traceable standards. This will give you confidence that the calibration is correct. In our incubator example an NIST traceable thermometer should be used to verify temperature.
After IQ you should have documented assurance that the instrument is received as designed and specified and has been properly installed in the user environment.
In our example, your incubator is now installed in your facility, connected to gas supply, turned on, configured as necessary for the alarm system, and calibrated appropriately.
Operational qualifications (OQ)
Now that your equipment is installed, the function of the equipment needs to be documented. This can be done by testing new samples or split samples and data analysis. During this phase of instrument qualification, you are establishing the stability of the equipment and validating the performance of the equipment.
In our incubator example, the first operation qualification task would be to document gas concentrations, temperature, recovery times, and stability with an empty incubator followed by an incubator with maximum specimens in it.
The result for analytical equipment is data on the 7 performance characteristics of precision, accuracy, linearity, limits of detection, specificity, reagent carryover if applicable and biologic reference intervals.
Training and skill development also occur during operational qualification, as well as establishing SOPs including for maintenance and use of the equipment.
In our example, technicians should be taught how to use the equipment and SOPs regarding the equipment use and maintenance should be established.
Operational qualifications should be repeated whenever a piece of equipment undergoes major repair, software update, or is moved to a new location.
Performance Qualifications (PQ)
Performance qualification documents the process consistently produces acceptable results under normal operations. This combines both installation and operational qualifications as well as day to day operations into one harmonious system. Performance qualifications should be performed whenever an instrument is in use.
Performance qualifications for our incubator would include daily quality control, data analysis to ensure the system is functioning to the agreed performance characteristics and on a consistent basis.
In our incubator example, PQ would be daily, weekly, monthly QC and data analysis of samples in the unit to confirm the unit is functioning and producing acceptable results.
If you purchase a new piece of equipment, consider investing in the IQ, OQ, PQ of that instrument. It will provide you with all the documentation you need for instrument qualification and help to achieve regulatory and quality requirements.
References:
- Process Validation General Principles and Practices. FDA Guidance Jan 2011 21 CFR 211.100
- The FDA and Worldwide Quality Systems Requirements Guidebook for Medical Devices. A. Daniel and E Kimmelman, Eds. Quality Press, Milwaukee, WI 2008
CRB News Articles
4/21/2020
Vol 9, No. 2
04/23/2020
Legal Considerations when Responding to the COVID19 Pandemic
04/23/2020
What is the Goal of Instrument Qualification?
04/23/2020
Be on the Lookout for an Important Survey Coming Your Way Soon!
04/23/2020
Are You Considering Becoming Board Certified? You Have Our Support
04/23/2020
Deadline for Recording Continuing Education Extended
04/23/2020
AAB/PEER Approved Continuing Education Programs
CRB Standing Rules - Log in to view